Description
The Screw pump has been designed for the transport of polymer solutions with a viscosity of up to 5,000 mPas. It is low-maintenance and can even be used if polymer solutions containing oil are to be metered.
Screw pumps, also known as progressing cavity pumps or helical screw pumps, are a type of positive displacement pump used to move liquids and slurries, particularly those with high viscosity, solids, or shear-sensitive properties. These pumps use a screw mechanism to move fluids through the pump chamber, offering steady, pulsation-free flow with minimal wear, making them ideal for transferring challenging materials.
Working Principle of Screw Pumps:
The basic principle of a screw pump involves a helical screw (or rotor) rotating inside a stationary stator. As the rotor turns, it moves the liquid or slurry along the screw’s length, pushing it from the inlet toward the outlet. This design allows for continuous and uniform flow, even with highly viscous or thick liquids, and ensures that the liquid remains undisturbed (non-shear), which is particularly important for sensitive fluids.
Main Components of a Screw Pump:
- Rotor: The rotating helical screw, which is typically made from hardened steel or stainless steel, depending on the application.
- Stator: A rubber or elastomeric sleeve that fits around the rotor, creating cavities where the fluid is trapped and moved forward by the rotor.
- Suction and Discharge Ports: The inlet and outlet for the fluid, which are positioned at opposite ends of the pump housing.
Types of Screw Pumps:
- Single-Screw Pumps (Helical Rotor Pumps):
- These pumps have a single helical rotor inside a cylindrical stator. The rotor creates cavities that trap and move the fluid as the rotor turns.
- Commonly used in pumping heavy oils, lubricants, and other viscous fluids.
- Twin-Screw Pumps (Dual-Screw or Intermeshing Screw Pumps):
- These pumps feature two intermeshing rotors that turn in opposite directions. As the screws rotate, the fluid is moved along the length of the screws, typically providing a smoother, more uniform flow compared to single-screw pumps.
- Often used in applications that require higher flow rates and efficiency, such as in the chemical, oil, and food industries.
- Triple-Screw Pumps:
- Similar to twin-screw pumps, but with three rotors instead of two. They are designed to handle very high-viscosity fluids and high-pressure applications.
- Common in high-performance applications, such as hydraulic systems, lubricating oil systems, and fuel transfer.
Advantages of Screw Pumps:
- Handling High Viscosity Liquids: Screw pumps are particularly effective for pumping thick, viscous fluids like oils, pastes, adhesives, and sludges. They can also pump fluids with a high solid content or shear-sensitive liquids, which might be damaged by other types of pumps.
- Steady, Pulsation-Free Flow: One of the major advantages of screw pumps is that they provide a steady, uniform flow with little to no pulsation, which is important in applications requiring smooth, continuous delivery of fluid.
- Self-Priming: Many screw pumps are self-priming, meaning they can start pumping without the need for external priming or a separate priming system. This is especially beneficial in applications where the pump may run dry or when the system needs to be started quickly.
- Versatility: Screw pumps are suitable for a wide range of fluids, including abrasive slurries, shear-sensitive liquids, oils, fuel, and chemicals. They can handle both high and low-flow rates, and their design makes them versatile for many industrial applications.
- Non-Shear Pumping: Unlike centrifugal pumps, which can damage or break down shear-sensitive fluids, screw pumps move fluids gently, preserving their integrity.
- Low Maintenance: Screw pumps are relatively easy to maintain because they have fewer moving parts than some other pump types. They also tend to wear evenly, which increases their lifespan.
Applications of Screw Pumps:
Screw pumps are used in a variety of industries, including:
- Oil & Gas:
- Crude Oil and Fuel Transfer: Screw pumps are commonly used in the oil and gas industry to transfer viscous crude oil, lubricants, and other hydrocarbons.
- Fuel Pumping: For transferring fuel and other viscous fluids in fueling systems and refineries.
- Water & Wastewater Treatment:
- Sludge Pumping: Screw pumps are used to handle thick sludge in wastewater treatment plants, where other pumps might struggle with solids or high viscosity.
- Sewage and Slurry: They are also used for pumping sewage and other slurry-like materials.
- Food & Beverage:
- Pumping Oils, Syrups, and Purees: In the food processing industry, screw pumps are used to pump oils, syrups, fruit purees, and other viscous food products that require gentle handling.
- Chemical & Pharmaceutical:
- Chemical Transfer: Screw pumps are ideal for transferring chemicals, adhesives, paints, and coatings. Their design ensures that even abrasive or sensitive chemicals can be transferred safely.
- Pharmaceuticals: In the pharmaceutical industry, screw pumps handle substances that require precise and gentle movement, such as creams, ointments, and gels.
- Marine and Industrial Lubrication:
- Lubricating Oil Systems: Screw pumps are used in lubrication systems for machinery and engines, where they ensure a consistent and steady flow of lubricant.
- Agriculture:
- Irrigation Systems: In agriculture, screw pumps are used to inject fertilizers, pesticides, and herbicides into irrigation systems.
- Pulp and Paper:
- Slurry and Paper Stock Transfer: In the pulp and paper industry, screw pumps are used to move paper slurry, pulp, and other materials in the production process.
Key Features of Screw Pumps:
- Pressure Handling: Screw pumps can handle moderate to high pressures, depending on the design, making them suitable for both low-pressure and high-pressure applications.
- Flow Rate: The flow rate of a screw pump is generally consistent and can be easily adjusted by controlling the speed of the rotor.
- Material Compatibility: The rotor and stator can be made from various materials such as stainless steel, cast iron, or specialized alloys, depending on the fluid being pumped (e.g., abrasive or corrosive fluids).
- Compact Design: Screw pumps tend to have a relatively small and compact design, making them suitable for applications with space constraints.
Conclusion:
Screw pumps are versatile, reliable, and efficient solutions for handling a wide variety of liquids, especially viscous, abrasive, or shear-sensitive fluids. Their ability to deliver steady, pulsation-free flow makes them ideal for applications across industries like oil and gas, wastewater treatment, food processing, chemicals, and pharmaceuticals. Whether for transferring oil, sludge, adhesives, or syrups, screw pumps provide smooth, continuous pumping with minimal maintenance requirements.
If you need more details or recommendations for specific screw pumps, feel free to ask!
Your benefits of Screw Pumps
-
1. Low-pulsation pumping
-
2. Feed rate is proportional to the speed
-
3. Reversible pumping direction
- FKM stator
- Stainless steel (Cr-Ni-Mo 17-12-2) rotor
- Stainless steel housing for 12/2 – 12/100
- Grey cast iron housing for 6/300 – 3/12000
- Axial face seal
- Voltage: 3-phase, 230/400 VAC
- Degree of protection: IP55
Screw Pumps Types
There different types of screw pumps are available in the market in different designs. They are briefly discussed below.
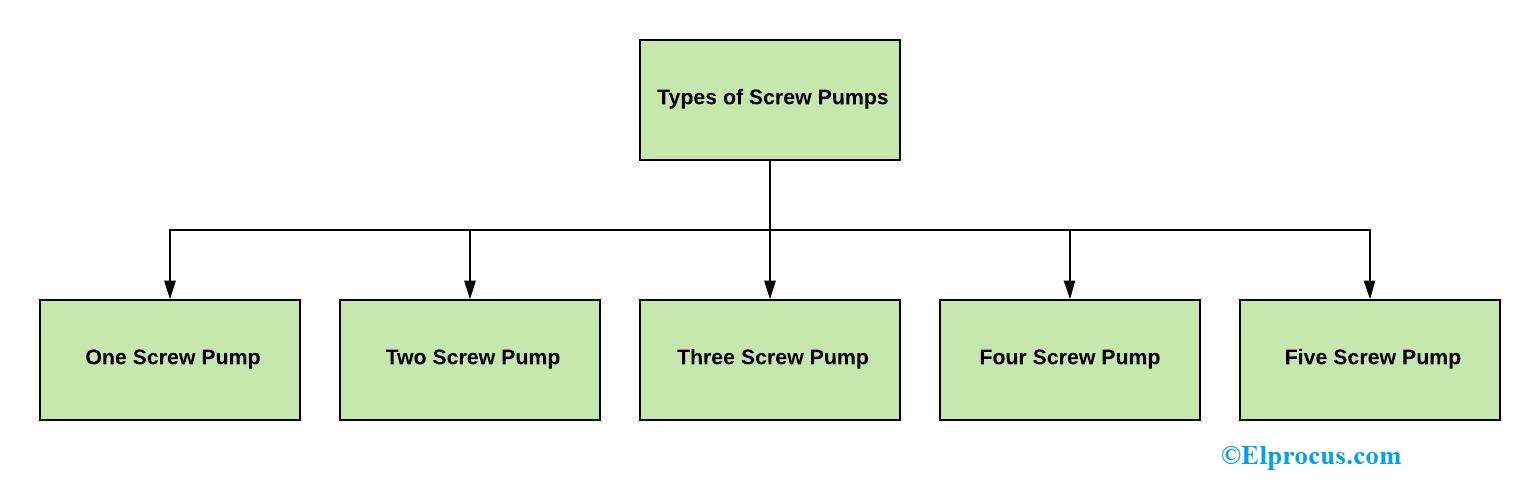
One-Screw Pump
These pumps are named as PC pumps otherwise progressive cavity pumps, and worm Pumps. Generally, these types of pumps are not considered within the family of the screw-pump. Because the rotor in these pumps are not like a usual screw but somewhat a twisted round shaft. A progressive cavity pump includes one shaft with somewhat twisted within the form of a screw, & is enclosed within a pumping hall that is generally rubber lined.
Two Screw Pump
These pumps are also named as the double screw pump, and it is the most general type used high power applications like weighty oil tube transfer. The screws in the pumps are driven from the motor, & timing gears are generally included to turn the next screw.
Three Screw Pump
These pumps are also named as the triple screw pumps, and these are usually used in small applications like lubrication systems. The screws in the pump are determined from the motor to rotate the remaining two screws which are around it without using timing gears.
Four Screw Pump
These pumps are basically two screw pumps, however with two screws for each rotor in opposite directions. These pumps absorb the liquid within the suction port, then divides evenly & is routed to both pumps ends.
The two liquids flow with the help of the pump towards the center & connect jointly again before leaving the release port. Similar to the double screw pump, this pump includes a timing mechanism to make the second rotor run. These pumps are frequently used within Multi-phase applications & oil transport pipelines.
Five-Screw Pump
These pumps are mostly similar like a triple screw pump; however with five screws, not three screws. Similar to the 3 screw pump, this pump includes one diving rotor that drives all the remaining screws. This type of pump is frequently used in many applications like tube oil otherwise hydraulic.
Screw Pumps Applications
The applications of screw pumps include the following.
- These pumps have many uses in a variety of applications in industries like oil, manufacturing, gas, and mining.
- Most of the pump applications are high viscosity fluids like asphalt, otherwise oil, multi-stage liquid, which means there is fluid and steam mixed jointly within the liquid stream.
- Some of the examples of these pumps used in systems include Multi-phase Pumping, Lubrication, Hydraulic Systems, and Weighty Oil pipelines.
Advantages/Disadvantages
To define there are many screw pump advantages and disadvantages.
Advantages
- These are used in any type of liquid medium
- Most effective to generate non-pulsating and constant results
- It holds the benefit to provide steady flow with varying back force
- The pump is completely noise-free also at extended pressure and rpm levels
- It holds the advantage of generating extended volumetric efficiency
- Regulated output, minimal maintenance and fewer vibrations too
Disadvantages
- Too costly to be implemented in small industries
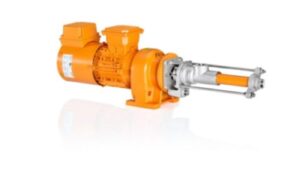